Introduction: The Role of Sinker EDM in Toolmaking
Sinker EDM (Electrical Discharge Machining) is a critical yet time-intensive process used to create intricate mold features like deep ribs and sharp internal corners, which conventional milling struggles to achieve. It involves creating precisely shaped electrodes (generally from graphite or copper) which are sunk into the conductive workpiece submerged in a dielectric fluid.
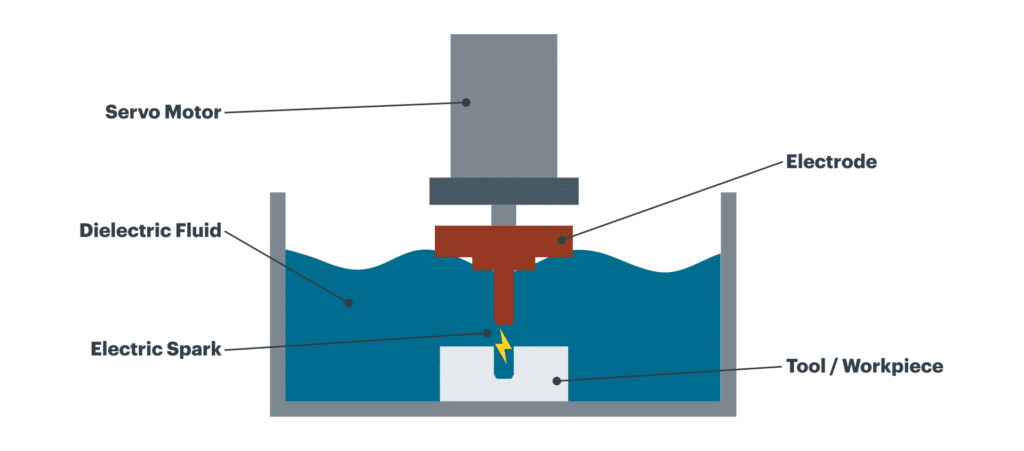
Challenges of Sinker EDM in Traditional Mold Manufacturing
While essential for manufacturing complex geometries such as irregularly shaped blind features, traditional sinker EDM comes with significant drawbacks: high costs, slow processing times, and substantial capital investment. A skilled workforce is also required to design and machine the electrodes and manage the EDM process.
Mantle’s customers tell us sinker EDM is the most time-consuming and expensive aspect of traditional mold building. Producing complex cavities and core inserts can require dozens of electrodes, making EDM a necessary but burdensome step. Fortunately, Mantle’s automated toolmaking system can significantly reduce this burden.
Mantle's Game-Changing Approach to eliminate sinker edm
Mantle has developed a groundbreaking approach that fundamentally reimagines toolmaking by integrating advanced 3D printing and precision machining technologies. Our system eliminates or dramatically reduces the need for sinker EDM, offering manufacturers a more efficient and cost-effective solution for the fabrication of components with deep features and tight tolerances.
- Alternating Additive and Subtractive:
Mantle’s technology first lays down a layer of tool steel paste, which is only 150 microns thick. Immediately after printing, the paste layer is dried to firm the layer. That layer is then machined flat, resulting in a perfectly flat, rigid, 100-micron layer. After printing ten layers, the resulting 1 mm paste layer is machined contour milled using traditional CNC machining tools and strategies. This process is then repeated to build the entire tool. Through alternative printing and machining, incredibly deep ribs and blind features can be formed.
- Ultra-Fine Machining Capabilities:
Mantle’s system utilizes traditional CNC machining technology and cutting tools as small as 0.006-inch ball end mills. These small tools leave a corner radii of less than 0.003 inches, often considered “EDM sharp” in the toolmaking industry.
- Soft Material Machining Advantage: During the shaping phase, the printed parts are in a ‘green’ state—with a density similar to foam. This dramatically reduces cutting forces, allowing the use of smaller tools without the risk of tool deflection or breakage and very fast machining. The minimal force on tools ensures deep and delicate features can be machined efficiently, a task typically reserved for EDM.
- Reduced Tool Reach Issues: By alternating between machining and incremental printing, Mantle’s technology addresses limitations in tool reach, a common challenge when machining deep mold sections.
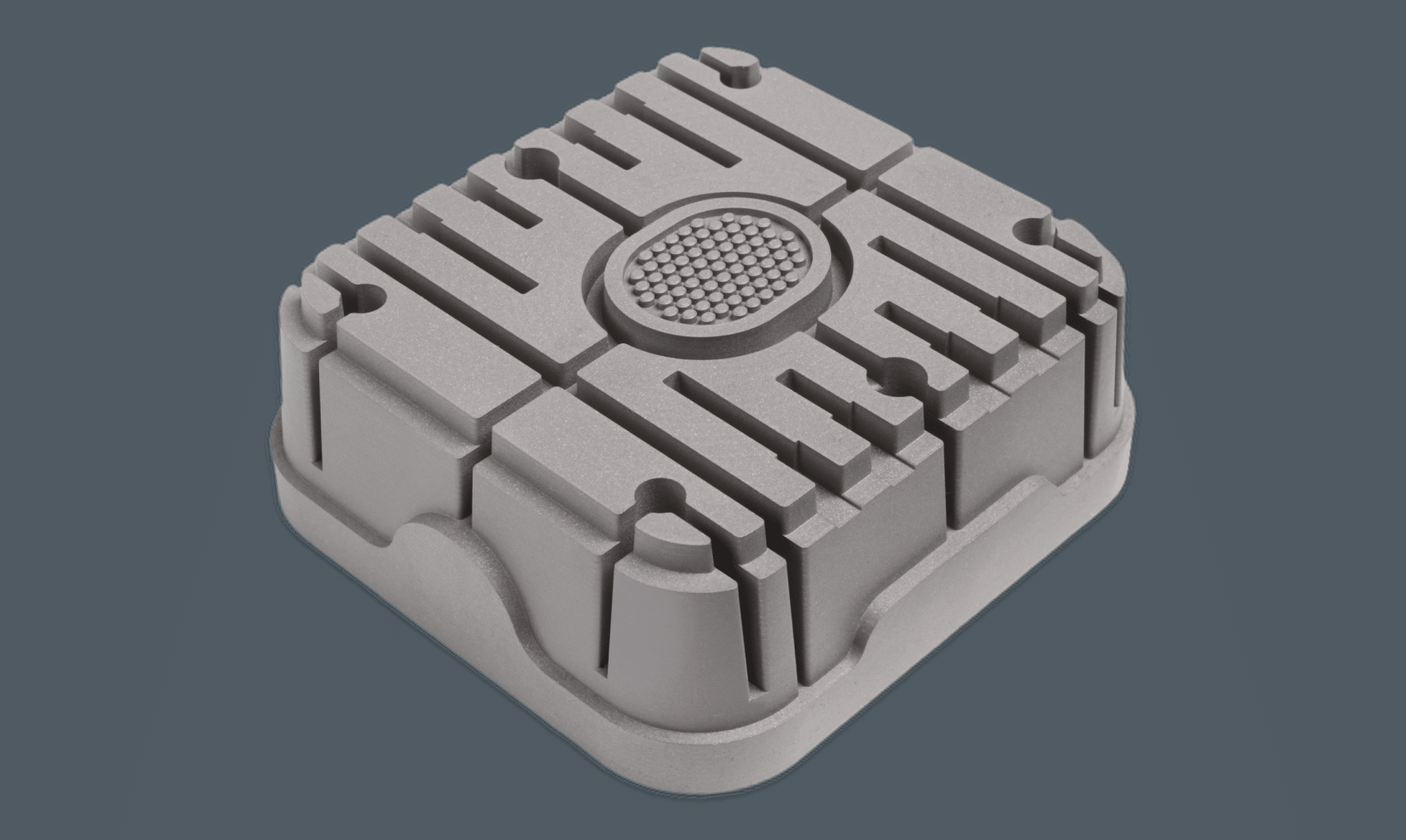
Real-World sinker edm elimination
180 HOURS OF SINKER EDM TO ZERO

Xpress7 worked with Westminster Tool to use Mantle’s metal 3D printing technology to produce a complex H13 tool steel mold insert, eliminating 180 hours of sinker EDM and shaving 2 weeks off the lead time.
Real-World sinker edm elimination
100 HOURS OF SINKER EDM TO 27
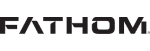
For a medical device mold, Fathom reduced the sinker EDM time from 100 to just 27 hours, an efficiency gain that freed their toolmakers to focus on other high-value tasks and resulted in a 40% lead time savings.
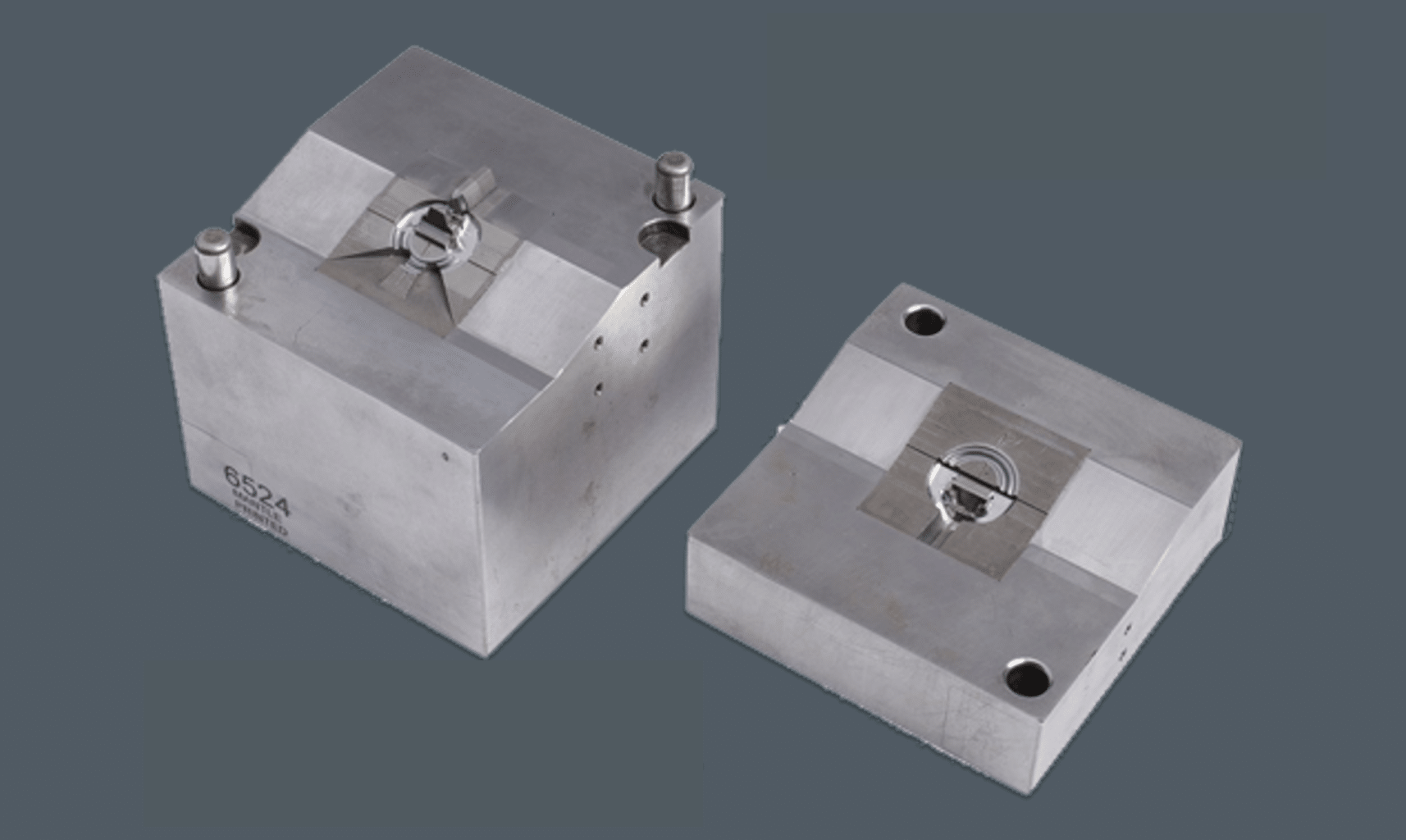
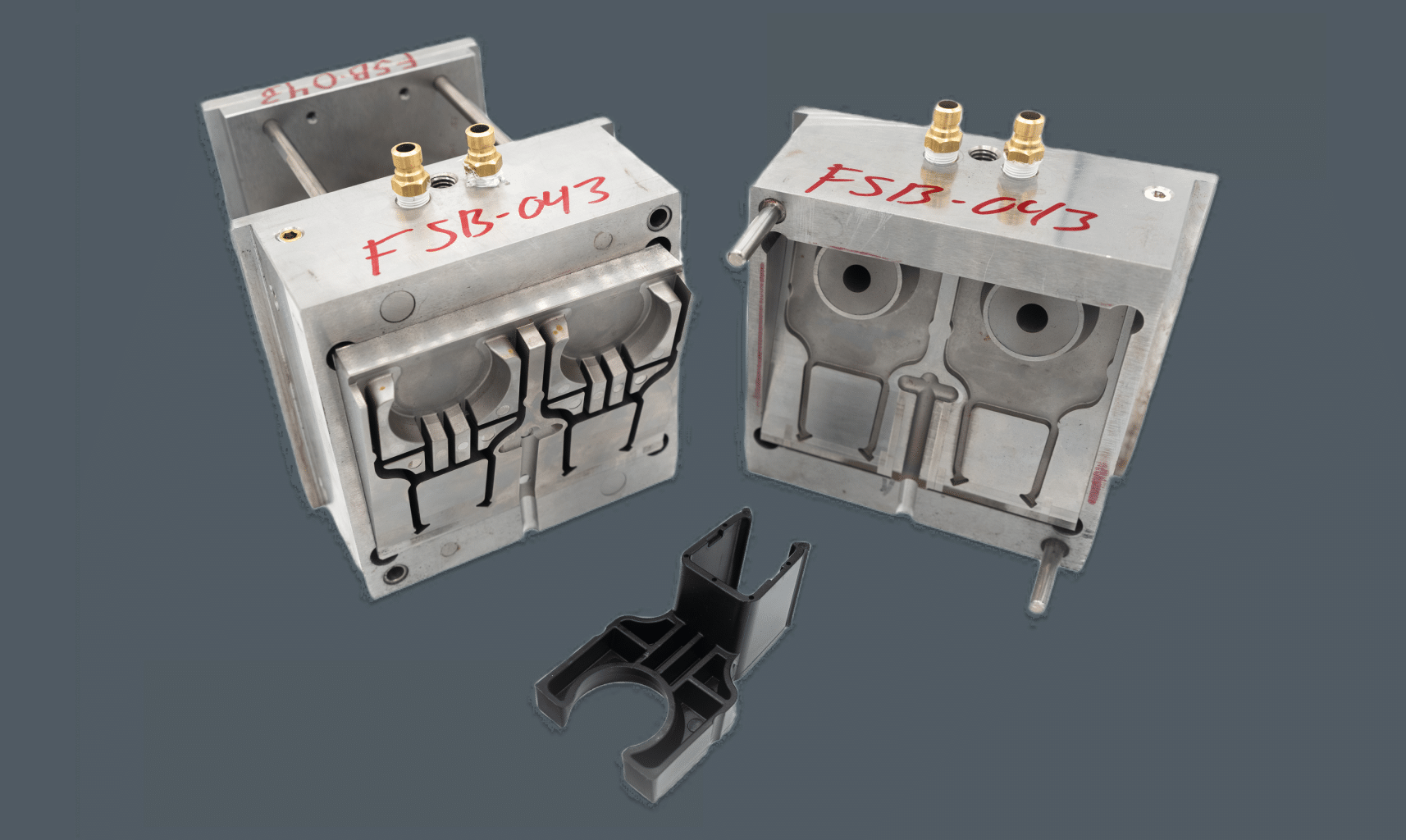
Real-World sinker edm elimination
40+ Hours of sinker edm eliminated
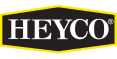
This is a consumer product that traditionally required extensive EDM and multiple electrodes to produce the deep ribbed features. Additionally, the parting line is at 15 degrees, which adds to the complexity of producing the inserts traditionally.
Conclusion: The Future of Toolmaking Beyond Sinker EDM
Mantle’s innovative approach to toolmaking is redefining industry standards by minimizing or eliminating the need for sinker EDM, which is traditionally one of the most time-consuming and costly steps in mold manufacturing. By combining advanced 3D printing with precision machining, Mantle empowers manufacturers to achieve unprecedented efficiency and accuracy in their processes.
Mantle’s technology dramatically reduces tooling lead times and costs by eliminating electrode design, programming, machining, and the sinker EDM burning process.
Are you ready to leave sinker EDM behind and explore a more efficient path forward? Contact our team today to discover how Mantle’s automated toolmaking technology can transform your toolroom.