DON’T LET THE TOOLMAKER SHORTAGE SLOW YOU DOWN
Hiring a toolmaker is more challenging than ever. Manufacturers struggle to fill open positions as experienced skilled toolmakers retire and fewer young professionals enter the trade.
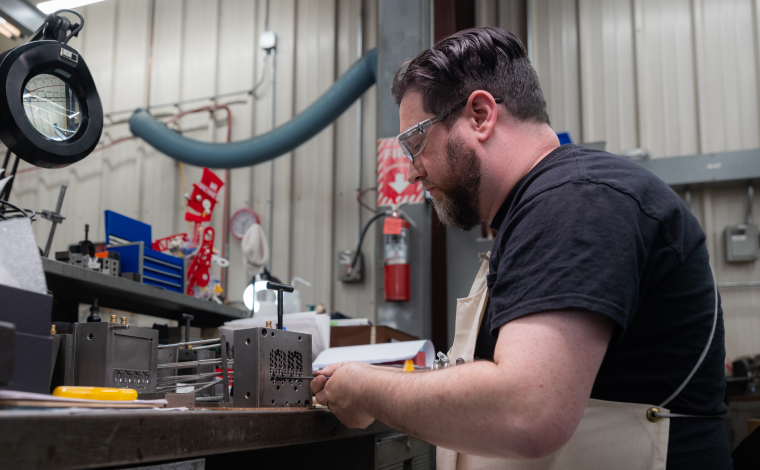
According to the quarterly National Association of Manufacturers (NAM) survey, a majority of manufacturers cite labor shortages among their biggest current business challenges. Skilled trades like toolmaking for injection molding can be among the most demanding roles to fill. This shortage bottlenecks operations, increases costs, and creates backlogs that impact production deadlines.
If your company has searched to hire a toolmaker without success, automation could help. Mantle’s automated toolmaking system helps increase capacity, reduce reliance on skilled labor, and keep production moving – even without new hires.
Here are five ways toolmaking automation helps fill the labor gap and maximize your business’ competitiveness.
1. EXPAND TOOLROOM CAPACITY WITHOUT HIRING A TOOLMAKER
Increase the capacity of your toolroom by automating up to 95% of a tool build with the push of a button. Streamline your tooling production workflows by easily creating ribs, deep pockets, or blind features during the tool build, eliminating the need for sinker EDM operations. Toolmaking automation also operates lights-out and requires minimal operator intervention for change over to keep production going – even during vacations or longer-term labor shortages. Mantle customers report that, on average, producing a tool using Mantle’s automated toolmaking system requires just 1.5 hours of active labor before the tool moves to finishing.
2. MAXIMIZE THE IMPACT OF EXISTING TOOLMAKERS
Instead of overloading your current team with long hours of tedious but low-value tasks like rough milling and fixturing, toolmaking automation can eliminate these repetitive tasks and allow your toolmakers to focus on high-value work where their expertise has the most impact, like final finishing. And automated toolmaking doesn’t stop when employees clock out, creating a more efficient toolroom and increasing overall throughput.
3. ACCELERATE TOOL PRODUCTION & REDUCE LEAD TIMES
With labor shortages, tooling often becomes the bottleneck to design validation and mass production. Automating toolmaking helps by cutting tool builds by weeks to reduce lead times and get parts to market faster. Eliminating bottlenecks caused by understaffed and backlogged toolrooms allows manufacturers to meet deadlines and take on more jobs.
4. UNLOCK PROCESS EFFICIENCIES
The ROI of toolmaking automation is further enhanced by the repeatable accuracy of automated production and through unlocking the benefits of conformal cooling. As part of its hybrid CNC-additive manufacturing system, the automated toolmaking process deposits and shapes tool steel, efficiently creating internal channels to help reduce cycle times, enhance process stability, and extend tool life.
5. MAKE YOUR COMPANY MORE COMPETITIVE TO WIN MORE BUSINESS
The inability to hire a toolmaker is one of the biggest challenges facing manufacturers. The toolmaking labor shortage makes scaling up operations through conventional means increasingly difficult. Relying on traditional toolmaking methods alone is no longer a sustainable path for growth. Investing in toolmaking automation allows companies to maximize the impact of their current staff, expand capacity without increasing labor costs, and meet growing production demands despite hiring challenges.
THE FUTURE OF INJECTION MOLD TOOLMAKING: PEOPLE + AUTOMATION
Automated toolmaking doesn’t replace your toolmakers – it empowers them. Struggling to hire a toolmaker? It might be time to think beyond traditional methods. Reach out to talk to one of our experts on your unique challenges and send us your tool design to take the Toolmaker Alternative Challenge and see for yourself how injection mold toolmaking automation can help.