introduction
Hear how Heyco Products dramatically accelerates product development using Mantle’s automated toolmaking system.
About Heyco Products
Founded in 1926, Heyco Products is a leading manufacturer of wire management systems, providing cable mounts, bushings, clamps, and other wiring components.
Heyco serves industrial, commercial, and residential markets. Operating 24/7 out of a state-of-the-art facility with 33 molding machines (ranging from 55 to 310 tons), the company consistently delivers reliable solutions worldwide while striving to improve efficiency and meet evolving customer demands.
CASE STUDY:
wire management/wire routing components
Key Results:
- Mantle molded parts fit form and function were equivalent to the conventional tool
- Printed an entire duplicate mold to double the cavitation
- All cavity feature detail left as printed
- 750k+ cycles, 3M+ parts
- Saved 2+ weeks
- Saved 60% of the cost compared to producing the tool traditionally
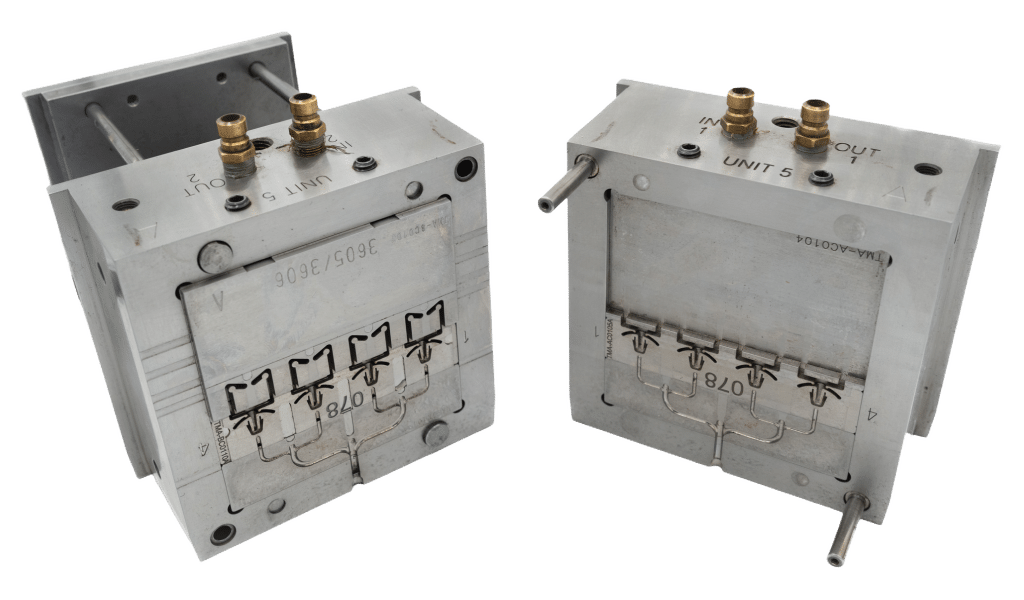
CASE STUDY:
threaded insert
Internally and externally threaded components for a new product design. Heyco needed to make a change to the external thread, so printed new inserts with Mantle in H13 tool steel.
Key Results:
- Printed in 2 days
- 3-4 hours of toolmaker time
- Squaring of insert and tapping of holes
- Threads left as printed
- Fully functional NPT threads that gauged and sealed properly
- Saved 2+ weeks
CASE STUDY:
consumer product
This is a consumer product that traditionally required extensive EDM and multiple electrodes to produce the deep ribbed features. Additionally, the parting line is at 15 degrees, which adds to the complexity of producing the inserts traditionally.
Key Results:
- Printed with Mantle in H13 tool steel
- Minimal finishing after printing:
- Squared inserts and tapped through holes
- All cavity feature detail left as printed
Saved 40-60 hours of sinker EDM time
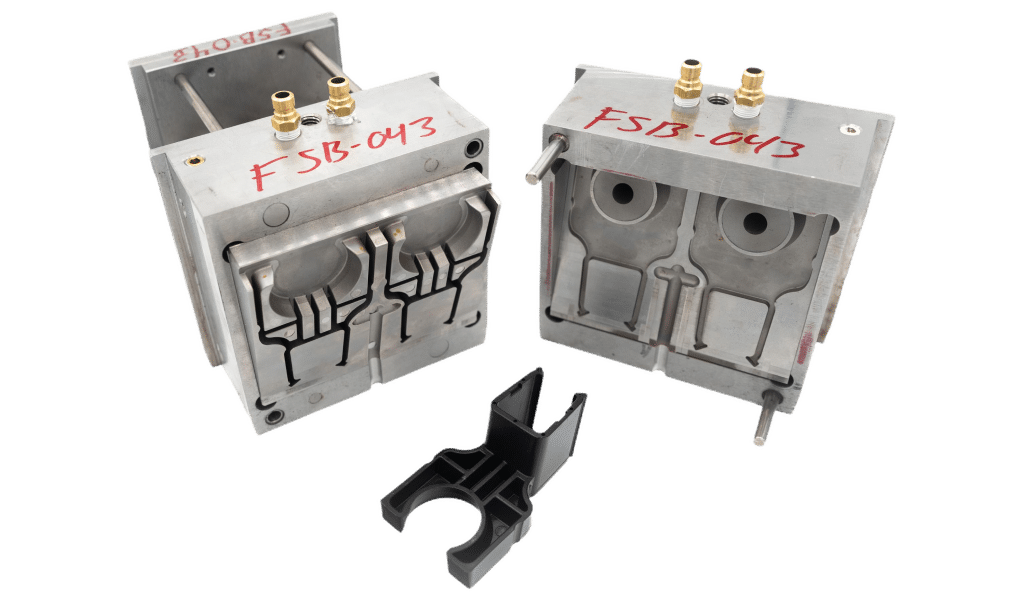