
Mantle’s software automatically calculates the additive and subtractive toolpaths for your tool.
Followers of metal 3D printing usually hear a lot about a company’s materials and printing technology – and much has been written already about Mantle’s Flowable Metal Pastes and our TrueShape printing process. But as industrial equipment users know, it is often the equipment’s software that can really make a difference in how well or poorly the technology is implemented—be it at a small machine shop or a global contract manufacturer.
MANTLE’S 3D PRINTED TOOLING
When we started designing Mantle’s metal 3D printing technology with integrated CNC machining, we aimed to reduce the lead times and costs to create tooling significantly. We knew that our system would have to hold very tight tolerances and produce very fine surface finishes using common tool steels that toolmakers use every day.
However, we also wanted to ensure the technology was as practical and easy-to-use, so toolmakers didn’t need to dedicate the time of their priceless 30-year veteran to generate the additive and subtractive toolpaths needed to achieve this precision. Hence, Mantle began with a plan to make our software as smart as possible to automatically generate toolpaths from the CAD files that were fed into it—without requiring the printer operator to have any CNC programming skills.
AUTOMATING THE TOOLPATHING PROCESS
We’ve made our system so simple to use that an operator merely uploads CAD files, selects the desired material, and hits print. No specialized programming skills are required. Our software automatically calculates all the toolpaths needed to print and shape the part. It also automatically calculates the sinter shrinkage rates and adjusts the printing dimensions. The software makes in-situ adjustments to ensure every tool produced meets toolmakings requirements for precision and quality.
The result is skilled programmers are freed up to do other important things in the shop, and a company can use the printer immediately to produce tools—not wait a year to get a specialist up to speed on how to program and operate it.
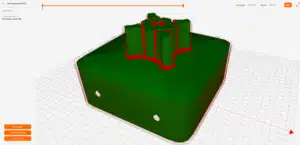
Mantle’s software selects different cutting tools based on the geometry and the process step.
CAPABILITIES THAT IMPROVE OVER TIME
Mantle also knew from the start that we wanted to add machine learning capabilities to the system’s architecture so each printer would get smarter over time, and all printers tethered to our software would help the entire system get smarter. We’ve designed our software platform to be Industry 4.0 / Internet of Things (IoT) compliant, to provide full traceability, and to provide real-time monitoring of each print—which translates to improved print and printer reliability and uptime.
All the sensors and cameras in our printers are connected to our software. The software constantly looks for print defects and compares the toolpathing that was planned with what is occurring to measure any deviation. If the difference is significant enough, it alerts the operator, who can stop the printer, review the data, and choose whether to back up and reprint a section of the tool. The result: accurate, precise 3D printed tooling without requiring programming skills or extensive post-processing.
There’s much more to tell you about Mantle’s software platform, and our capabilities will continue to evolve, so we’ll share more in future posts.
ADVANTAGES OF MANTLE’S SOFTWARE PLATFORM
- Automatically generate additive and subtractive (CNC) toolpaths without the operator needing to be a skilled CNC programmer
- Operations are simple: upload approved CAD files, select desired material, and hit print
- Real-time machine and print monitoring to ensure quality
- Automatic compensation for shrinkage to ensure accurate parts
- Machine learning to help each printer get smarter over time
- Industry 4.0 / IoT compliant