MANTLE’S METAL 3D PRINTED MATERIAL ACHIEVES RESULTS EQUIVALENT OR SUPERIOR TO STANDARD P20 TOOLING STEEL
Mantle, a company whose proprietary metal 3D printing technology makes high-precision parts for the tooling industry, today released a comprehensive study on its P2X material performance. The P2X Material Performance Study includes the results of testing performed by third parties on Mantle’s P20-comparable steel. The tests assessed the behavior of P2X in typical tooling operations and compared it to the performance of standard P20 steel. Results show that Mantle’s P2X material performance is equivalent or superior to standard P20 steel.
The studies performed included:
Tool Modification Performance
While Mantle’s TrueShape™ technology produces highly accurate tools, these tools may still require modification to address engineering changes or to prepare inserts for a mold base. The following tool modification operations were performed with P2X material and compared to standard P20 tool steel:
- Milling and drilling: equivalent to standard P20
- Machining and grinding: equivalent to standard P20 and far more stable than laser-based additive parts
- Welding: equivalent to standard P20
- EDM: equivalent to standard P20
The stability of this material is amazing. I was expecting it to constantly move around like laser-based additive parts do. Machining operations with this material are very predictable.
Ray Coombs
President, Westminster Tool
Surface Finish Operations Performance
Mantle’s TrueShape™ technology produces inserts with a smooth matte surface finish suitable for molding. Inserts can be further finished with texturing and polishing. Polishing studies included a variety of techniques, including stone, diamond, and paste polishing. Texturing studies included acid and laser etching. In all cases, P2X performed just like standard P20 and could be polished to an A2 polish.
This material took texturing just like P20 with the same settings. We could polish it to an A2 finish.
Mold-Tech
Hardness, Thermal Conductivity, and Corrosion Resistance
Optimal molding performance requires molds that are durable so they can withstand hundreds of thousands to millions of shots. Hardness testing was performed with the Rockwell C procedure; results showed that P2X is slightly harder than standard P20 tooling steel.
Tooling materials also require known thermal properties so heat transfer can be designed and managed. P2X’s thermal resistance is lower than the thermal resistance of standard P20, but Mantle’s TrueShape™ process can create conformal cooling channels for superior thermal management.
Tool steels must also resist corrosion when exposed to certain substances, including water, which passes through internal cooling channels. Test blocks of P2X and standard P20 steel were submerged in water for 4 days to assess corrosion. Significant corrosion occurred with P20 tooling steel. Only minor corrosion occurred with P2X.
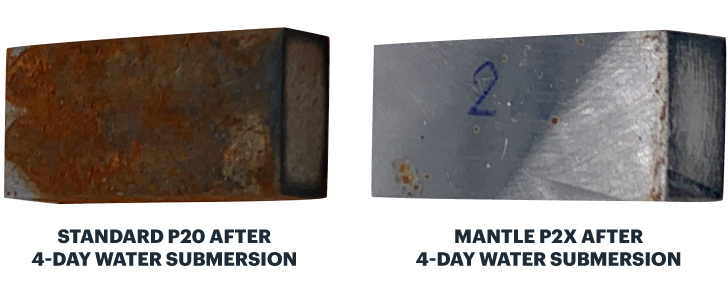
Low Volume Production Run with Abrasive Material
Molders must also understand how a tool wears under standard conditions when molding with abrasive materials. A low volume production run was performed using one insert made with P2X and another insert made with standard P20 tooling steel. The molding conditions were identical and the plastic material used was a 40% glass-filled and 25% mineral-filled nylon. Inserts made with Mantle P2X showed 42% less wear than standard P20 tool steel over the same number of shots.
The complete P2X Material Performance Study may be found here. These studies confirm that Mantle’s P2X material and TrueShape™ metal additive manufacturing process produce molds with the material properties, accuracy, and surface finish required to meet the needs of the demanding tooling industry.