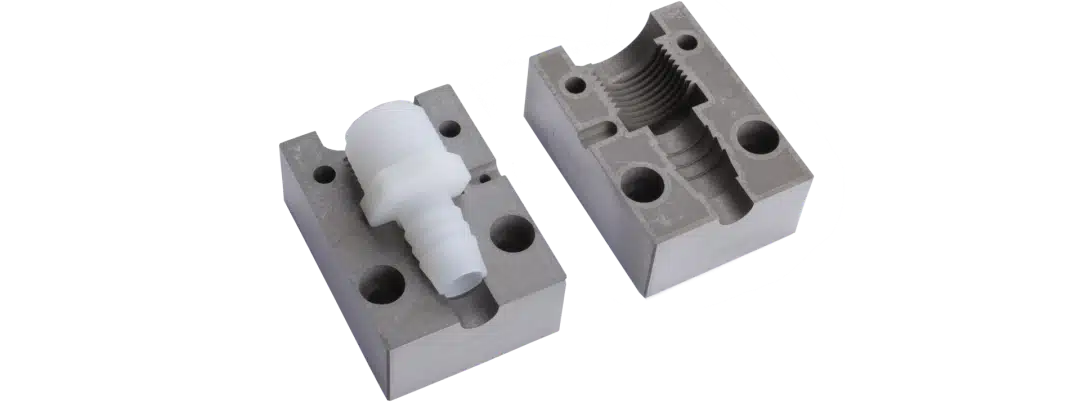
PROTOTYPE TOOLING
RAPID INJECTION MOLD PROTOTYPE TOOLING
Mantle-printed prototype tooling enables production-equivalent parts early in product development processes. Steel production-representative tooling allows for true functional prototyping, manufacturing validation, trials, and certification.
If tool design changes are minimal, printed tools can then be used as bridge or production tools.
FUNCTIONAL PARTS
MANUFACTURING PROCESS
PRODUCT DEVELOPMENT
AND PRODUCTION
REAL FUNCTIONAL PARTS
Test confidently, knowing that even your most challenging materials – including PEEK, Acetal, Radel, heavily filled, and even metal – were made from production-representative tools.
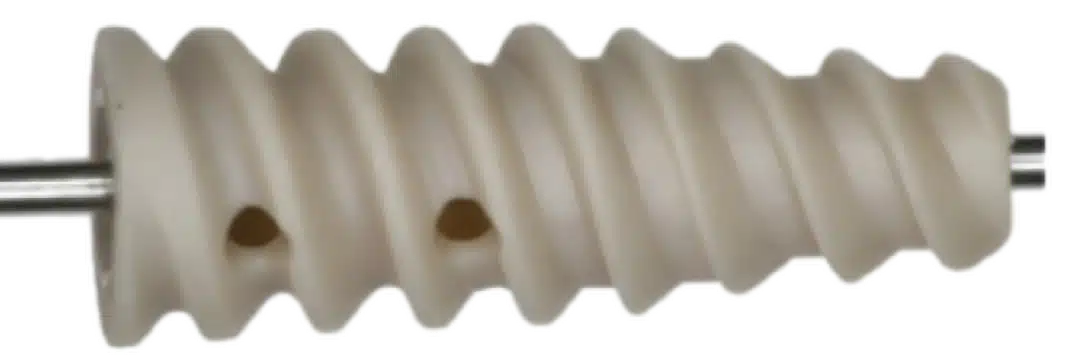
TOOL STEEL FOR BRIDGE TOOLING
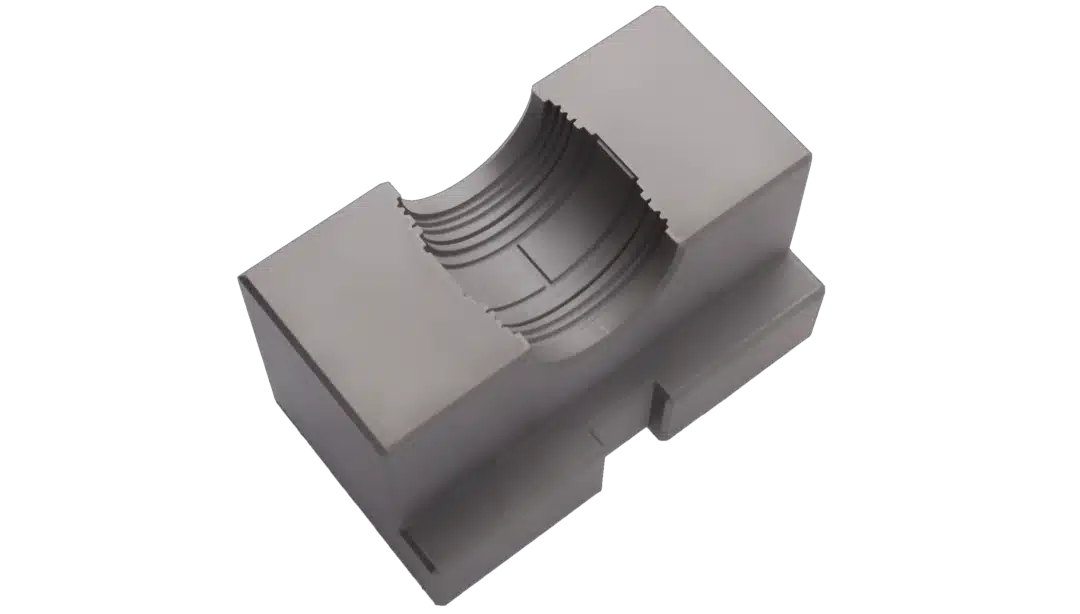
Production representative tooling
H13 tool steel for millions of cycles
Polish, texture, and repair
VALIDATE YOUR MANUFACTURING PROCESS
By using tool steel prototype tooling during the development stage, manufacturers de-risk their production molding by testing and validating critical process parameters such as plastic shrink rate, cycle time, and cooling rate.
- Validate plastic shrink rate
- Define molding process parameters
- Learn cycle time and cooling rate
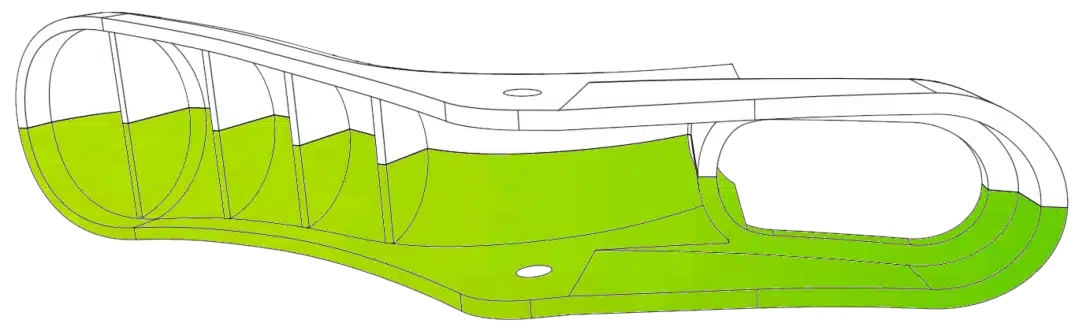
CASE STUDIES
FIRST PROTOTYPE LEAD TIME CUT BY 80% USING TOOL-STEEL MOLD FOR HIGH-TEMP PLASTIC PARTS
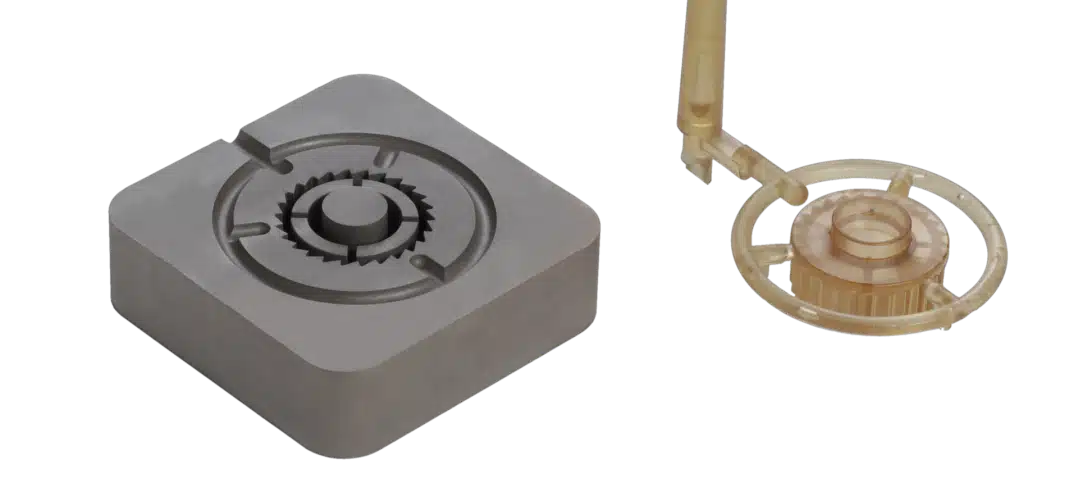
A global medical device manufacturer sought a solution to significantly reduce the time to prototype parts made with high-temperature plastic. Using Mantle, a cavity and core tool-steel inserts were printed in just over 2.5 days.
WESTEC PLASTICS PRODUCES H13 PROTOTYPE TOOLING FOR MEDICAL DEVICE COMPONENT IN 5 DAYS
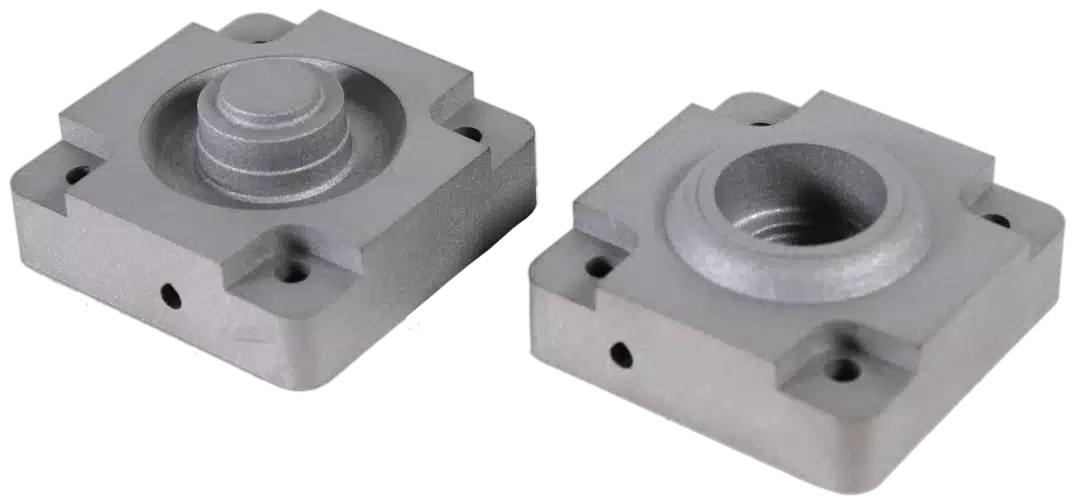
Westec Plastics used their Mantle metal 3D printer to print a set of H13 tool steel inserts for Gracon Manufacturing. Gracon Manufacturing was implementing a design change on a plastic part already in production, so needed to get tooling as quickly as possible to validate the design change.
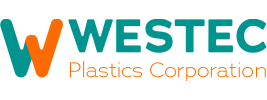
PROTOTYPE TOOLING FAQS
What is prototype tooling?
Prototype tooling is a cost-effective and time-efficient way to produce functional parts for testing, validation, and early-stage manufacturing. These tools often value speed and low cost over durability since they are designed for short runs. Still, they often need to mimic production tooling to ensure the parts produced with the tooling match those of the future production tool.
How is prototype tooling used?
Prototype tooling is a crucial step in product development, bridging the gap between design validation and full-scale production. After a part's form and fit have been validated—typically using CAD or a plastic 3D-printed prototype—prototype tooling is used to create functional parts using the final production manufacturing process that can be tested under real-world conditions.
Prototype tooling allows manufacturers to assess part functionality and material suitability, ensuring optimal performance while verifying efficient manufacturability using the intended production method (injection molding, die casting, MIM, etc.)
When should you use an Aluminum Prototype Tooling vs. a Steel Prototype Tooling?
Aluminum Prototype Tools
Aluminum tools are cost-effective and easy to machine, making them ideal for early-stage prototypes or when only a few parts are needed. They are typically used for low-pressure molding applications and less abrasive materials. While aluminum's great ability to conduct heat can be a benefit to cool a mold quickly, it can present challenges if you are eventually molding to a steel tool, as steel has a much lower heat transfer coefficient. Parts molded in an aluminum tool will be very different than steel, and you may find a part that molded well in an aluminum tool does not work in your production tool, as the difference in heat transfer can lead to different shrink rates, warping, and other molding defects.
Steel Prototype Tools
Steel tools, such as those made with Mantle’s technology, are better suited for prototyping engineering materials (abrasive-filled plastics, high temperature, etc.) required for higher-value applications such as regulated industries that require prototype parts for validation (such as FDA validation). Steel tools are ideal when validating part functionality, performance, and the production manufacturing process. They can also be directly used as bridge or production tools if no or minimal design changes are required.